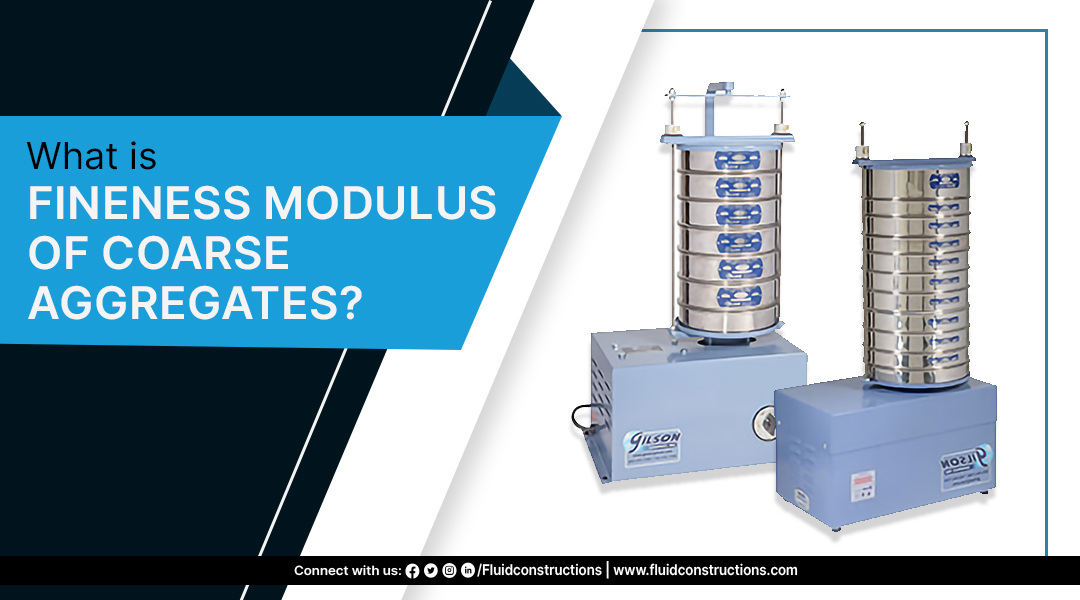
What is Fineness Modulus of Coarse Aggregates?
Aggregates play an important role in both cement concrete and bituminous concrete (asphalt), as they increase the mechanical strength of the mix. However, the different sizes and shapes of the particles used have an effect on the characteristics of the concrete. The fineness modulus of coarse aggregate determines the proportion of fine and coarse aggregates in a concrete mix to derive the quality and workability of the mix for a given application.
What are Aggregates in a Concrete Mix?
Aggregates are raw materials that are available naturally or extracted from pits and quarries, including gravel, crushed stone, and sand. They form an important component in making concrete along with cement and water, or bitumen. Depending on the size and shape of the particles, the aggregates, when used with binding mediums like cement, bitumen, and water, form compound materials such as asphalt concrete and Portland cement concrete.
Besides making the concrete strong, aggregates help lower the amount of cement used in concrete. In general, aggregates constitute 80% of a concrete mix. The water absorption capacity of aggregates also makes an important contribution to determining the strength of the concrete.
The material qualities of aggregates need to be consistent, uniform, and predictable. They need to be clean and dry before use. The proportion of fine and coarse aggregates in a concrete mix is specified by their fineness modulus (FM).
Different Types of Aggregates and How They Differ
There are two different kinds of aggregates: coarse aggregate and fine aggregate. Based on their granular sizes, each kind is further divided into various categories and classifications. A sieve analysis test is performed to determine if an aggregate sample is fine or coarse. If the sample particles pass through a No. 4 sieve, then it’s a fine aggregate; otherwise, it’s a coarse aggregate.
Coarse aggregates do not pass through the No. 4 sieve since their initial size is 0.19 inches. The distinctions between coarse and fine aggregates are explained in more detail below.
Fine Aggregate
Fine aggregates, which consist of crushed stones or other granular materials, form an essential part of concrete. Fine aggregate is defined as the particles that almost completely pass through the 4.75 mm (No. 4) sieve or completely pass through the 9.5 mm (3/8 in.) sieve but are retained on the 75 µm (No. 200) sieve. The maximum amount of water that fine aggregates can absorb is 3%. The hardened properties of the concrete are significantly influenced by the density and quality of the fine aggregate.
Coarse Aggregate
Coarse-grained aggregates will not pass through a No. 4 sieve with 4.75-mm openings. Particles that are predominantly retained on the 4.75 mm (No. 4) sieve and will pass through a 3-inch screen are called coarse aggregate. The coarser the aggregate, the more economical the mix.
The properties of the coarse aggregates used determine the properties of the concrete mix. The water absorption of coarse aggregates in any climatic condition should not be more than 2%. As for the size of the coarse aggregates, the larger the particles, the smaller the total surface area to be wetted. And less paste is required for lubricating the surface to reduce internal friction. This reduces both cement and water requirements in a concrete mix.
Further, since there is less water requirement, less pore water is present in the void spaces. This results in less evaporation and, therefore, reduced drying shrinkage. The angularity and strength of the particles also affect the concrete in numerous ways.
The table below provides more differences between the two:
Sl No | Scopes | Fine Aggregate (FA) | Coarse Aggregate (CA) |
1 | Definition | Small-sized filler materials used in construction are called fine aggregates. | Larger-sized filler materials used in construction are called coarse aggregates. |
2 | Size of Particles | The particles that stay on a 0.075 mm screen after passing through a 4.75 mm filter are known as fine aggregates. | The particles that remain on a 4.75 mm sieve are known as coarse aggregates. |
3 | Materials | Fine aggregates used in concrete include sand, surki, stone screens, burnt clays, cinders, fly ash, etc. | Coarse aggregate in concrete can be made of broken bricks, broken stones, gravel, pebbles, clinkers, cinders, etc. |
4 | Sources | The main sources of fine aggregate are crushed stone, crushed gravel, and river or machine sand. | The main sources of coarse aggregate are natural rock disintegration, crushed stone or gravel, and dolomite aggregates. |
5 | Surface Area to be wetted | More surface area in the mix to be wetted. | Coarse aggregates cause less surface area in the mix to be wetted. |
6 | Function in Concrete | Fine aggregate fills in the spaces left after the coarse aggregates are filled. | For concrete, coarse aggregate serves as an inert filler. |
7 | Uses | Layer filling in road pavement, plaster, concrete, and mortar all require fine aggregates. | The principal applications for coarse aggregates are in ballast for railway tracks and concrete. |
How Fineness Modulus Affects Concrete Mixes
Not all concrete is the same. Although they all have the three fundamental elements, cement, aggregate, and water, each batch of concrete can differ significantly from the next based on the proportions and amounts of these three constituents.
Fineness modulus (FM) is a value that indexes the average size of aggregate particles used in concrete. The size of the particles has a significant impact on how quickly the concrete pours and spreads, as well as its strength and durability once cured. A higher value of FM indicates coarse aggregates, i.e., bigger particles.
The fineness modulus enables concrete contractors to accurately forecast the amount of water required to mix the concrete. It also accurately depicts the workability of the concrete, which is assessed in terms of slump value. In general, the higher the fineness modulus, the greater the slump value—or, in other words, the stiffer the concrete.
The fineness modulus also offers vital information regarding the density and compressive strength of the resultant concrete. Both of these elements must be considered while designing the concrete. An FM of fine aggregate between 2.5 and 3.0 produces concrete that is easy to put together, easy to finish, and less likely to crack in most mixtures.