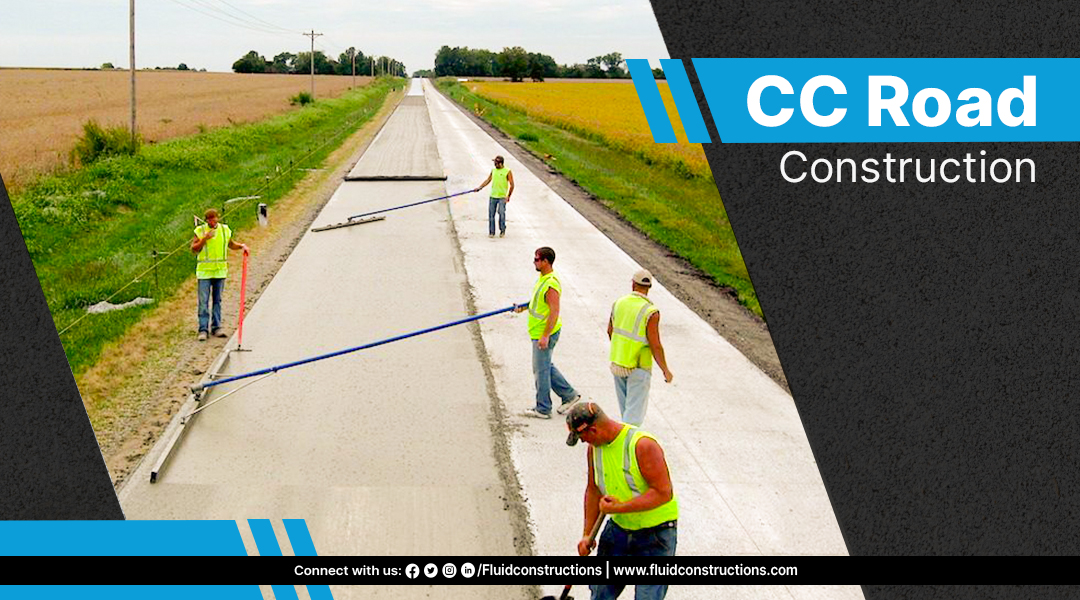
CC Road Construction – An Overview
Of all road types, if you have to select the most rugged and durable one, waste no time and go for CC roads. Despite its high initial cost, the CC, or cement concrete road, is fast becoming the default road type in India, both in urban and rural areas. Why? Find out in this quick read on CC road construction.
Cement concrete roads are built with a mixture of Portland cement, coarse aggregate, sand, and water. The most significant benefit of a concrete road is its long service life (20 to 30 years) due to its outstanding resilience.
For the same reason, they are much less prone to wear and tear flaws such as rutting, cracking, stripping, texture loss, and potholes that can occur on macadam or asphalt pavement surfaces. As a result, cement concrete demands very little maintenance and therefore proves to be more economical.
Well-constructed cement concrete pavements require little or no upkeep throughout their lifespan. Less maintenance also means less traffic delays, which is a big benefit on some of our already overcrowded highways.
Another significant benefit of cement concrete pavement is that it causes less fuel consumption by the traffic, resulting in a 14–20% reduction in fuel cost. This one reason alone can justify the construction of a long stretch of CC road.
The desirable properties of a cement concrete road
- Proper thickness is needed to distribute wheel load to a safe value on subgrade soil.
- Durable enough to endure all types of stresses – traffic loads, heavy rainfall, water logging, etc.
- Sufficient coefficient of friction to prevent skidding of the wheel
- Smooth surface for a better driving experience.
- Impervious surface to protect the subgrade soil.
- Long life at a minimal cost of maintenance
- The thickness should be sufficient to transmit and distribute the applied loads over a broader region of the soil underneath.
- A surface that can resist abrasion induced by vehicle tyres.
There are 3 types of CC roads, namely JPCP, JRCP, and CRCP.
JPCP (Jointed Plain Concrete Pavement)
This type uses contraction joints and no reinforcing steel for better control against cracking.
The spacing between transverse joints is so chosen that temperature and moisture forces do not cause intermediate cracking between joints.
JRCP (Jointed Reinforced Concrete Pavement)
JRCP employs steel mesh reinforcement (also known as dispersed steel). JRCP designers purposefully increase joint spacing and use reinforcing steel to hold mid-panel cracks together.
CRCP (Continuously Reinforced Concrete Pavement)
CRCP uses continuous, longitudinal steel reinforcement without transverse joints, except for header joints wherever necessary at the end of the day, especially at bridge approaches and at transition points to other pavement constructions. Continuous reinforcement is a technique to manage transverse cracking that occurs in all new cement concrete pavements.
CC Road Construction Methods
CC roads are built in two or three layers. The standard practice involves the following CC road construction layers:
- Surface course: This is the top layer, which is made of the PCC or plain cement concrete slab.
- Base course: This layer runs just below the PCC layer and is often composed of aggregate or stabilised subgrade.
- Subbase course: The layer (or layers) beneath the base layer. However, a subbase is not always required.
Surface layer
The surface course or layer is made of homogeneously mixed PCC. This is the layer that comes in contact with traffic loads and therefore demands properties like friction, smoothness, noise management, and drainage.
It acts as a waterproofing layer for the base, subbase, and subgrade. The thickness of the surface course may vary, although it is typically between 150 mm (6 inches) for light traffic loads to 300 mm (12 inches) for heavy traffic loads.
Base layer
The base layer lies directly beneath the surface layer, made up of stabilised aggregate or soil, lean concrete, and dense and permeable HMAs. It helps in
- Distribution of additional loads
- Drainage and frost resistance
- Uniform support for surface-layer pavement
The base layer also serves as a stable foundation for construction equipment and helps in the prevention of subgrade soil movement caused by slab pumping.
Subbase layer
The subbase course is built, if required, between the base course and the subgrade. It generally serves as structural support, but it also helps in:
- Reducing the penetration of fines from the subgrade into the surface layer
- Improving the drainage
- Reduce the impact of frost
The subbase layer is made up of lower-quality aggregates than the base course and high-quality structural fill.
The following steps are involved in the construction of a CC road:
- Site preparation: This entails clearing and levelling the earth to provide a strong foundation for the road.
- Subgrade preparation: Aggregate and soil are laid and compacted to provide a sturdy foundation for the surface concrete layer.
- Formwork: Form (mould) is used to give the shape of the road.
- Reinforcement: Steel rods are used in the formwork to reinforce the strength of the road.
- Concrete placement: Mixing and pouring cement concrete into the formwork, which is then levelled and compressed to remove any air bubbles.
- Curing: To attain maximum strength, the concrete is allowed to cure for a few days.
- Finishing: This involves using trowels to remove tiny particles to create a smooth surface.
Methods of Surface Layer Construction
Depending on the various factors, the surface layer is constructed using one of the following two processes:
Alternate Bay Method.
The alternate bay method is carried out in alternate bays. The bays or slabs are built in an alternate sequence (A and C in the above figure), leaving the intermediate bays (B and D). These intermediate bays are built after a minimum of one week if standard Portland cement is used and two days if rapid-hardening cement is used. This strategy is feasible and effective when the projected width of the pavement exceeds 4.5 m. This strategy improves working efficiency when placing slabs.
Continuous Construction Method
This method involves all bays or slabs built continuously without a break. Construction joints are corrected when the day’s work is completed. Dummy joints are also used at 5-metre intervals in the transverse direction to locate the weak spots and prevent cracking. This method is often chosen over the alternate bay method because it allows for the building of half the pavement width at a time and helps traffic movement over the opposite side of the road.
Hope, you have got your answer and also other important information about CC road construction. If you want to know more about our construction company , please write to us at [email protected]
Image source:
https://www.ques10.com/p/49933/state-the-methods-of-construction-of-cement-conc-1/