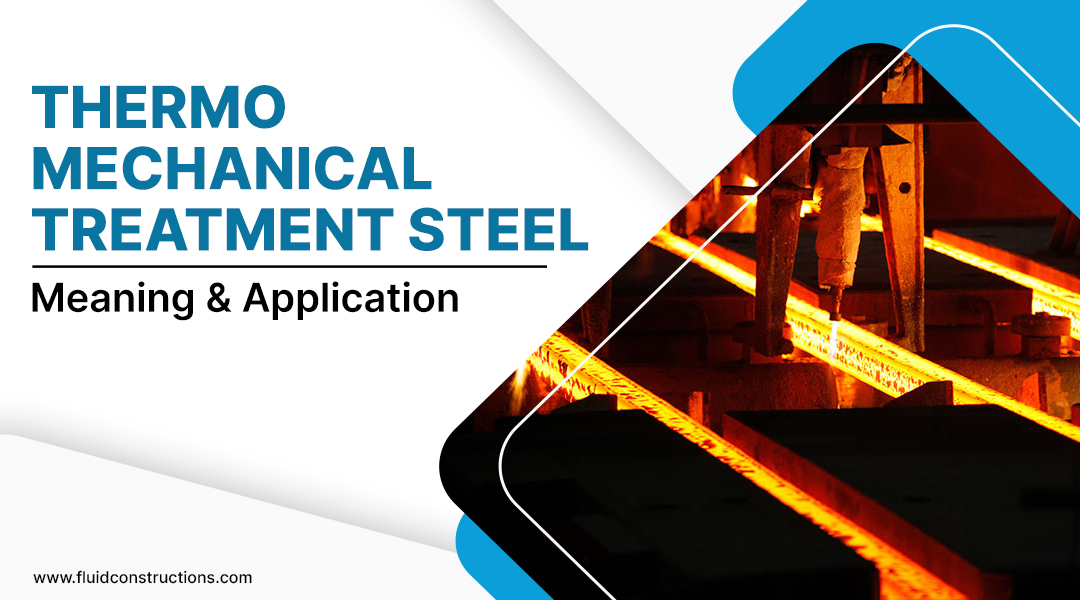
Thermo Mechanical Treatment Steel: Meaning and application
Both concrete and steel form the body mass of construction-concrete as mussels, steel as bones. That explains why thermo-mechanical treatment steel production is driving the GDP of India, meeting its massive infrastructural push.
From earthquake-resistant highrises to dams and bridges to marine structures, TMT steel bars are playing a critical role in transforming the face of RCC structures, making them more resilient and long-lasting.
What is TMT steel?
TMT steel is a special form of steel, produced through a metallurgical process called thermo-electric treatment, for use in the construction industry. The TMT steel bars have a soft inner core and a tough outer surface, which make them strong yet flexible in their characteristics. Also, they are highly resistant to corrosion and rust.
What is thermo-mechanical treatment?
Thermo-mechanical treatment is a metallurgical process that combines thermal processes like heat treatment and water quenching with mechanical processes like forging, rolling, etc. This is the technology behind the production of TMT steel bars. The steps involved in producing TMT steel bars are as follows:
Heating, rolling, and forming of reinforced bar: Steel billets are heated to roughly 1200 °C (2192 F) to 1250 °C (2282 F) to transform into reinforced bar (rebar) before passing through a rolling mill stand to attain the final shape and size.
Quenching: When the hot-reinforced bar exits the final rolling mill stand, it is instantly quenched- a sort of heat treatment in which the rebars are rapidly cooled by water in a quenching box to achieve specific material qualities.
The abrupt temperature shift toughens the outer layer of the steel bar, increasing its tensile strength and endurance. Sudden quenching causes the steel bar’s surface to become cold and martensite (hardened), while the core remains hot.
Self-tempering: After leaving the quenching box, a temperature gradient forms through the quenched bar’s cross-section. Heat flows from the hotter inner core to the colder outer Martensite surface, transforming it into a tempered Martensite structure.
Natural cooling: When the self-tempering ends, the rebars are subjected to ambient cooling to equalize the temperature difference between the soft inner core and the tough outer surface. When the bars cool down completely, the soft interior core transforms into a ductile structure.
What makes TMT steel the first choice in construction?
- No compromise in strength: The carbon content of TMT bars is kept at 0.2%. This maintains strength without compromising weldability.
- Easy weldability: Joints of TMT rods can be welded using regular electrodes without the need for additional safety measures.
- High ductility: They are very ductile because of their soft innards and strong exteriors.
TMT bars are affordable and safe to use because they meet all three of the critical requirements: strength, weldability, and ductility. An added benefit of TMT bars is their resistance to corrosion since the cooling process prevents the formation of coarse carbide. Also, seismic loading is increased by the soft ferrite pearlite. TMT bars are often made in the following grades: Fe-415, Fe-500, Fe-550, Fe 500D, and Fe 550D. Their standard lengths range from 5.5 to 13 meters, and their diameters start at 8, 10, 12, 16, 20, 25, 28, 32, 36, and 40 mm.
Advantages of thermo mechanical treatment of steel
- Increased strength and ductility: The exceptional strength of the bars makes them an appropriate material for use with concrete to strengthen structures. The TMT bars’ unique ribbed pattern adds strength by connecting them more closely with concrete. TMT bars’ ductility makes them easier to bend and create meshes. Pre-welded meshes may be easily built off-site, saving overall construction time.
- Anti-rust properties: The TMT manufacturing process gives the bars anti-rust qualities. Coarse carbides, the main cause of corrosion in steel, are prevented from forming during the water-quenching stage. This ensures the long life of the structures built using TMT steel bars and rods.
- Increased fire resistance: TMT steel can endure temperatures ranging from 400 to 600 degrees Celsius because of its great thermal stability, ensuring the structural integrity of the building even during a fire.
- Earthquake resistance: The soft core of the TMT bars imparts a high amount of flexibility, allowing structures made with TMT steel to better manage dynamic and seismic loading.
- Cost saving: TMT bars offer much higher tensile strength and elongation value, which means you need less steel for the same volume of structure. This saves money on shipping and storage, in addition to lowering the cost of raw materials. TMT steel bars are also easier to control on-site, resulting in additional cost savings due to decreased construction and fabrication time.
Applications of TMT steel
- Extensive use in construction: TMT bars are predominantly utilised in the construction of residential and commercial structures, bridges, and all other infrastructure projects. TMT bars are used as reinforcing steel bars in concrete structures to boost the structure’s strength and durability.
- TMT bars can be utilised as tension members in a variety of structures, including suspension bridges, cranes, and tower masts.
- Because of their strength and ductility, TMT bars are perfect for use in columns.
- TMT bars are frequently employed in the beams, which support floors and roofs.
- TMT bars are used in the building of lintels, which are beams that sustain the weight of the structure above doorways and windows.
- TMT bars are employed in pre-stressed concrete. This puts the concrete beams under a load that is higher than the load they will be expected to sustain.
- TMT bars have better resistance to seismic forces than other types of steel, making them perfect for construction in earthquake-prone areas.
- TMT bars are frequently used in the building of industrial buildings, including power plants, warehouses, and factories.