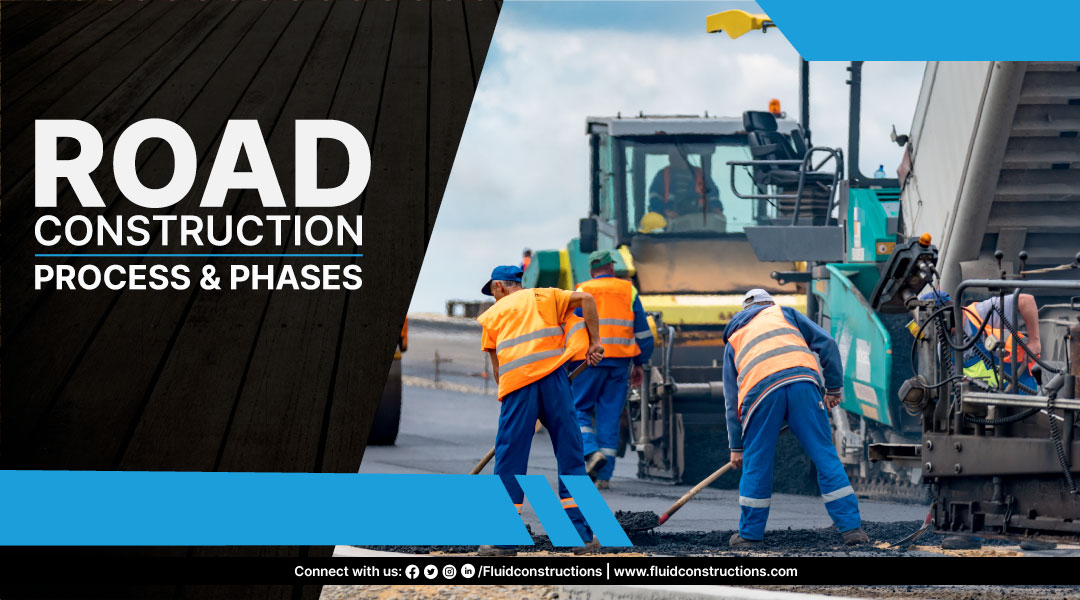
Road Construction Process and Phases
A road is not just a strip of asphalt or concrete, but a harbinger of development in an area. Therefore, road construction must be strong enough to withstand the environmental effects and the surge in traffic influx in the years to come.
Road construction is a time-consuming process that may take years to finish, depending on the distance between the places to connect. It necessitates rigorous planning and evaluation, including environmental and structural analyses, and deployment of several teams of crews and plant equipment.
The purpose of road construction is to serve the connected areas for a prolonged period of time. Therefore, maintenance of the road has become as important as its construction. So, when we look at the lifecycle of road construction, it’s divided into some functional phases which include maintenance as well. We’ll come to that later in this blog, but for now let’s first understand how a road is constructed.
What are the Road Construction Processes?
The modern road construction process involves the removal of natural impediments as well as the use of new types of building materials that are far more durable and long-lasting. Also, when building a new road, it is critical to create a pavement structure that is extremely well-bonded, beginning with a firm foundation layer and proceeding all the way up to a carefully leveled top course. Let’s look at the various steps:
1. Cleaning up the Current Base Course Layer
To prepare the current surface, remove any corrosion or potholes that may be present. Premix chippings are used to fill in the imperfections at least a week before the surface course is laid. Instead of directly placing a bituminous concrete surface course on a WBM when the existing pavement is extremely thin, a bituminous leveling course of sufficient thickness is provided.
2. Utilising Tuck Coat
The placement of the AC (asphalt content) layer over a bituminous base or binder course is preferred. For non-bituminous bases, this amount may be increased to 7.5 to 10 kg when applying the tack coat of bitumen, which is applied at a rate of 6.0 to 7.5 kg per 10 sq.m.
3. Preparation and Placement of Premix
The premix is created in a hot mix plant with the desired level of quality control and the necessary capacity. The aggregate temperature shouldn’t deviate from the binder temperature by more than 14 degrees Celsius, and the bitumen can be heated to between 150 and 177 degrees Celsius.
A mechanized paver spreads the hot mixed material at a temperature of 121 to 163 degrees Celsius after being gathered from the mixture by the transporters, who also precisely measure the camber and layer thickness. The strength of the final pavement structure is greatly influenced by temperature management during mixing and compaction.
4. Rolling
Rolling at a speed of no more than 5 km/h thoroughly compacts a mix after it has been deposited on the base course. The first or breakdown rolling is carried out by an 8–12 tonne roller, and the intermediate rolling is carried out by a 15–30 tonne fixed wheel pneumatic roller with a 7 kg per sq. cm tire pressure.
The roller’s wheels are kept wet with water. The number of passes necessary varies depending on the layer thickness. If the initial rolling was insufficient in warm weather, rolling again the next day can help to improve the density. A tandem roller weighing 8 to 10 tonnes does the final rolling or finishing.
5. Bituminous Concrete Construction Quality Assurance
On-site routine inspections are done to make sure the final concrete mixture and pavement surface are of high quality. The following are periodically checked: a) Bitumen quality; b) aggregate temperature; c) aggregate temperature during mixing and compaction; d) temperature of paving mix.
For the aforementioned tests, at least one sample is taken and tested for every 100 tonnes of mix that the hot mix facility discharges. Also performed are Marshall tests. To determine whether the field density is at least 95% of the density found in the laboratory, one test of the field density is performed for every 100 sq.m of the compacted surface. 6mm per 4.5m of thickness fluctuation is permitted.
6. Checking of the Finished Surface
A 3.0 m straight edge should be used to inspect the AC surface. In a length of 300 m, the longitudinal undulations shouldn’t be more than 8.0 mm, and there shouldn’t be more than 10 undulations that are higher than 6.0 mm. Undulations in the cross-traffic profile shouldn’t be greater than 4.0mm.
What are the Road Construction Materials Used?
Road construction materials include soil, aggregates (coarse and fine), bitumen, binders, and admixtures. Every layer has complete control over how its own substance is applied. The numerous ways that materials for road construction can be used include the following:
The soil is used as a subgrade material, whether it is produced artificially or naturally.
The sub-base course is made up of a mixture of coarse and fine materials.
When mixed with bitumen, an aggregate measuring 0 to 10 mm in size acts as both the base course and the wearing course.
Bitumen is utilized in bitumen mixture, tack coat, and prime coat as cutback bitumen, emulsion, and asphalt.
What are the Various Phases in Road Construction?
Road construction projects are expensive and have different purposes to serve. They progress through different phases, meeting the stringent conditions and guidelines to fulfill their purposes throughout their lifecycle. The phases in a road construction project are:
- Planning
- Design
- Earthwork
- Quality Control
- Maintenance
Planning
Every project that involves the construction or upkeep of roads must start with careful planning and study of the requirements it must satisfy. To make sure they will actually get a decent return on their investment in construction, private companies should assess local traffic patterns, both present and future, and conduct a cost-benefit analysis. This will guarantee that they actually get a return on their investment. Possible issues with money, the law, and the environment will now be considered in order to find answers beforehand.
Design
The next stage of a typical building and maintenance project is the design phase. Surveyors will physically visit the site and use laser technology to precisely determine the alignment, shape, and direction of the road.
The location, terrain, and soil characteristics of the area, as well as the possibility of future expansion in the immediate physical vicinity, as well as any potential water access and drainage issues that may arise, are all taken into consideration during this phase of the project.
Earthwork
The area where the road will be built needs to be cleared of all vegetation and obstacles before any work is begun. Excavation vehicles should remove any trees, bushes, shrubs, boulders, and stones to make sure the ground is prepared for building.
After the topsoil is taken out, the subgrade should be examined to determine whether it can support the weight of a concrete road. Before building, the subsoil may be removed or stabilised if this stage reveals that it is insufficient.
Under the road embankment, sand wicks can be added to stabilize the subgrade. By shortening the distance that water must travel in a drainage system, these additions are beneficial. By capturing groundwater, sand drains, on the other hand, help to stabilize the subgrade.
The subgrade can also be strengthened by removing subpar cuttings and replacing them with carefully chosen fill. In addition to employing chemicals, cement, or bituminous materials, stabilization processes are also possible.
Quality Control
After the concrete road construction process is complete, the road should undergo a number of quality checks before being made accessible to the general public. Testing methods include drainage confirmation, level grading, and road reflectivity to evaluate the quality of roads.
The process of creating the road might be considered complete if it passes the assessments made. The road can now be used for transit and made open to traffic.
Maintenance
Traditional road surfaces will deteriorate over time due to environmental and traffic-related causes, necessitating their rehabilitation. The expected lifespan of road construction and maintenance projects varies from country to country, but on average, one can assume that the project will be in use for several decades, with considerable rehabilitation work being carried out every 10 years or so.
FAQs: Road Construction Processes and Phases
What is pavement?
Pavement refers to the durable surface layer constructed on roads, highways, or sidewalks to withstand traffic loads and provide a smooth driving surface.0
What are roads made of?
Roads are typically made of various materials, including asphalt, concrete, gravel, or a combination of these, depending on factors like traffic volume, climate, and budget.
What are the different methods of construction?
Road construction methods vary and may include asphalt paving, concrete paving, chip sealing, gravel grading, and more, each tailored to suit specific project requirements.
What is pavement in road construction?
In road construction, pavement refers to the top layer of the road surface designed to support vehicle loads and provide a smooth and safe driving surface for motorists.
What is rigid pavement?
Rigid pavement, also known as concrete pavement, is a type of road surface constructed using a layer of concrete. It offers high durability and structural strength, making it suitable for heavy traffic areas.
How to construct a road?
Road construction involves several phases, including planning, site preparation, earthwork, sub-base and base course construction, pavement laying, and finishing touches like signage and markings. The process requires coordination between engineers, contractors, and various stakeholders to ensure quality and safety.